Positioner
The welding robot positioner is an important part of the robot welding production line and welding flexibility plus unit.The equipment has a simple structure and can rotate or translate the welded workpiece to the best welding position. Usually, the welding robot uses two positioners, one for welding and the other for loading and unloading the workpiece.
electronics, and machinery, as well as CNC machine tools, spraying turntables and other customized machines that need to change the product position.
Welding positioners are divided into various types of deformers such as side positioners, return positioners, lifting positioners, double return positioners, etc. Users can customize them according to actual production needs. It can be arbitrarily matched with different welding equipment, and the combination is convenient. Introduce well-known coordinates to strictly inspect each part to improve product accuracy and service life. The equipment assembly and processing accuracy is greatly improved.
The robot positioner is used in conjunction with the manipulator and the welding machine to form an automatic welding center, and it can also be used for workpiece displacement during manual work. The welding positioner is generally composed of a worktable slewing mechanism and a turning mechanism. Through the lifting, turning and rotation of the worktable, the workpiece fixed on the worktable can reach the required welding assembly angle. The turning of the worktable adopts inverter stepless speed regulation. , High speed regulation accuracy. The remote control box can realize remote operation of the workbench, and can also be connected with the operating machine and the welding machine control system to realize linkage operation.
The three-axis horizontal turning positioner in the robot workstation is used to rotate the fixture and change the position of the two fixtures. The rotation range: ±180°. After the rotation is in place, it is accurately positioned pneumatically to ensure welding accuracy. During the welding process, the displacement of the fixture and the coordinated movement of the robot can turn any section of the weld to the most suitable welding position, and the robot drives the welding torch to weld in the best welding posture. Three-axis positioner + dual-machine linkage reduces welding distortion and makes work more efficient.
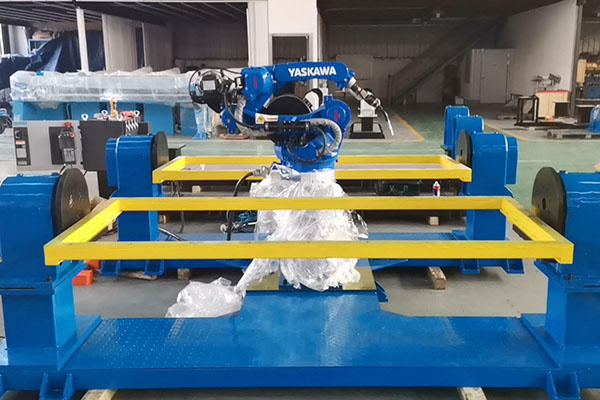
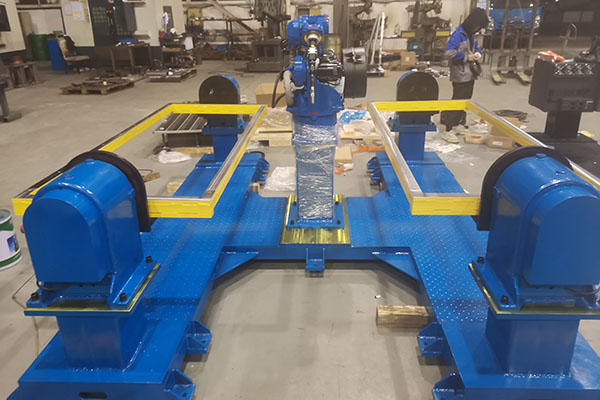
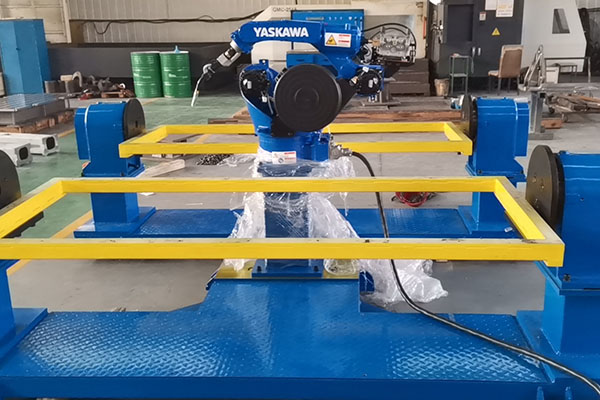

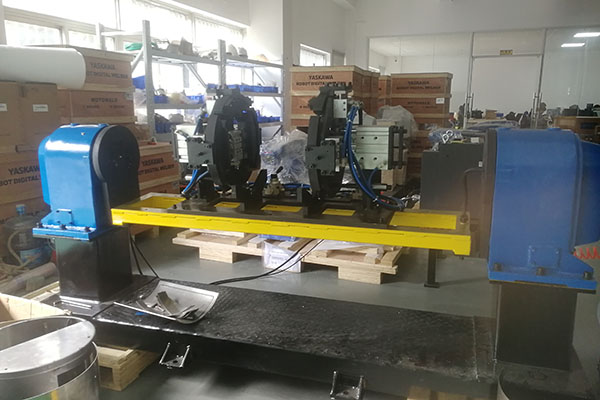
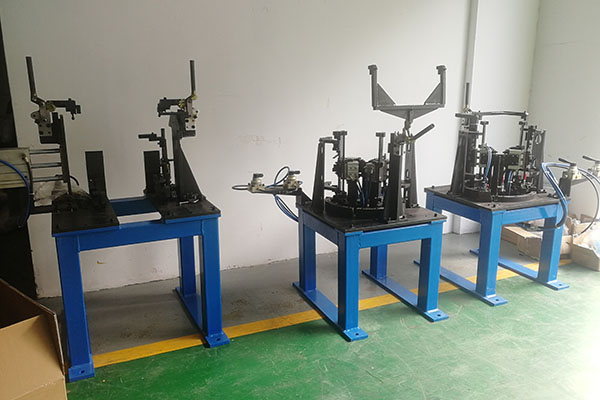